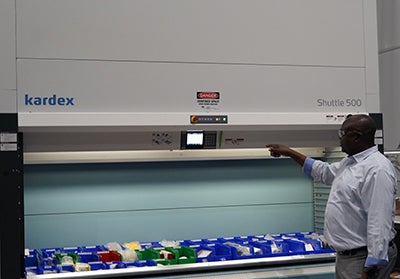
Camden’s logistics organization has added a new Automated Vertical Lift Module for additional capacity and efficiency
As Aerojet Rocketdyne, an L3Harris Technologies company, builds new facilities and transforms manufacturing processes to ramp up solid rocket motor production, its Camden, Arkansas, logistics team is also retooling its practices and upgrading its equipment to increase efficiency and keep the nearly 2,000-acre site running smoothly.
The logistics team’s role in solid rocket motor production process includes many activities, like moving raw materials to production lines, finished products to warehouses and goods to customers. The team also handles tooling calibration and inventory management to help the site meet its production schedules.
Senior Logistics Manager Kalumba Poshi leads the 40-person Camden logistics organization, which has undergone modernization efforts over the past 24 months that have improved inventory accuracy, supply chain efficiency and the delivery of raw materials and finished goods across the site.
One example includes reorganizing the kitting (small items) area to prioritize a lean U-shape kits build process. This has significantly boosted the speed at which the company assembles kits for various programs and prepares for increased production rates.
Overall, the Camden logistics organization manages ~30,000 line items with a total value of more than $400 million. Together, this team of managers, material handlers, analysts, dispatchers and truck drivers manages more than 350,000 material transactions annually that support solid rocket motor production.
That means the Camden logistics group manages material handling and delivery to more than 150 buildings and 24 satellite locations, including one main warehouse and 33 World War II-era energetic bunkers. Altogether, the logistics team oversees more than 330,000 square feet of storage and inventory space.
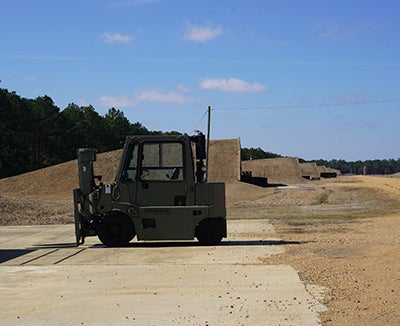
The solid rocket motor production site has also added new Swing master forklifts that can spin 360 degrees and provide maneuverability, productivity and safer transportation of large solid rocket motor cases into magazines
“We like to think of our team as the FedEx or the XPO of Aerojet Rocketdyne,” said Poshi, who joined Aerojet Rocketdyne in early 2021.
Among the modernization improvements to enhance production efficiency and safety are new optical sensors that provide high-speed and 3D scanning to better calibrate tooling. Other recent equipment upgrades include new delivery trucks and two rotary forklifts that can spin 360 degrees, maneuver in tight spaces and lift heavier materials. The advanced warehouse upgrades also include an automated vertical lift tool that can robotically retrieve and store inventory with the push of a button.
Altogether, the logistics organization has made upgrades and investments totaling $1.5 million over the past three years.
Director of Scheduling & Material Planning Rayna Creedon emphasized that the logistics function impacts the efficiency of every Aerojet Rocketdyne program and building and the site’s overall production. A good logistics team, she noted, plays a key role in managing a world-class manufacturing operation and providing quality products to customers on time.
“We will continue to refine our processes and leverage modern equipment to deliver the materials and tooling necessary for daily production on schedule and to the right building or location, to ensure our team can manufacture the solid rocket motors that are so critical to programs that support our warfighters,” said Creedon.