

Overview
L3Harris’ advanced reactor and thermal-hydraulic models unlock maximum fidelity and performance from your simulator. The models are based on first principles and advanced numerical techniques, and are extensively proven with installations worldwide.
Advanced Reactor Kinetics Models
Comet™ and Comet Plus™ are advanced models for the simulation of reactor neutron kinetics based on a rigorous application of first principle physics and advanced numerical techniques.
Comet™, primarily applied to the simulation of heavy water reactors (PHWRs), solves diffusion equations by using the Mesh-Centered Finite Difference (MCFD) method modified by the application of the Generalized Equivalence Theory in the calculation of homogenized parameters.
Comet Plus™, used for simulating light water reactors (LWRs) and gas-cooled reactors (GCRs), solves the diffusion equations by using the Nodal Expansion Method (NEM). The NEM represents the flux by a fourth-order polynomial and yields unprecedented accuracy.
Both Comet™ and Comet Plus™ are true three-dimensional models. A minimum of one radial node per fuel assembly/channel is used. The neutron diffusion equations are solved at each node at each time step without relying on approximate methods based on a space-time factorization.
Each node takes into account:
- Xenon, Iodine, Samarium and Promethium concentrations
- Six delayed neutron groups for LWRs and 15 for PHWRs
- Decay heat calculations are carried out using a set of 23 decay heat precursors
- Neutron source strength
- Fuel burn-up, plutonium build up and depletion of burnable poisons, if applicable
Control rods are treated as individual entities and shadowing effects are fully simulated. Variable enrichment fuel and other modern fuel designs can be accounted for.
The calculation of the flux at the in-core detector locations is achieved by reconstructing the flux, as a function of the local nuclear properties, in the nodes where detectors are present. Very localized effects, such as the effect of movements of neighboring rods on detector responses, are fully simulated.
Cycle-specific parameters are calculated by Orchid® Core Builder. This powerful tool features a user-friendly graphical interface in order to maximize ease of use. For example, adding a detector or changing the real-time model nodalization can easily be done graphically. Orchid® Core Builder also provides features allowing the user to rapidly validate the input lattice code neutronic data as well as the output real-time model parameters. Orchid® Core Builder accepts plant data from several typical lattice and fuel design codes such as CASMO, SIMULATE-3, ANC, SCIENCE and others. Finally, Orchid® Core Builder facilitates implementation of Recommendation 6 of INPO’s SOER 96-02 to provide cycle-specific simulator training. With Orchid® Core Builder’s Initial Condition (IC) Transfer mechanism, users can easily age core cycles without having to recreate ICs for each new core cycle update.
Advanced Steam Supply Model
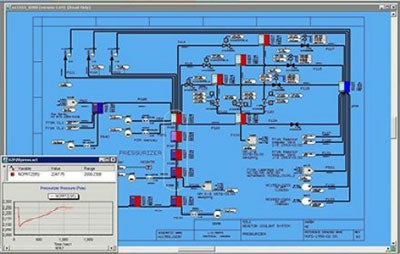
L3Harris' advanced thermal-hydraulic model (ANTHEM™) is based on a rigorous application of the equations of mass, momentum, and energy conservation and implicit numerical techniques. ANTHEM has been successfully installed and validated on numerous simulators and simulator upgrades currently certified for training.
ANTHEM™ has been specifically designed to ensure faithful real-time simulation of both single and two-phase flow under all plant operating conditions. The model accurately simulates:
- Normal and abnormal plant conditions
- Major transients such as steam line breaks, loss of feed water, tube leaks, load rejection and turbine trips
- Draining, filling and venting, as well as nuclear mid-loop operations
- A single model is used for all operations without switching to reduced nodalizations or simplified models. The model takes into account such phenomena as feed and bleed cooling, shrink and swell, loop seals, natural circulation, flow stagnation, local boiling and condensation, phase separation and the effect of local buildups of void or non-condensables.
ANTHEM™ is a non-equilibrium, non-homogeneous, drift flux model. The conservation equations consist of three mass conservation equations for liquid, water vapor and non-condensables, two energy equations for liquid and gas mixture and the momentum equation for the liquid gas mixture. The mass and energy equations are solved at each node and the momentum equation is solved at each link. The drift flux model is used to resolve gas and liquid velocities from the mixture momentum equation. Nodalization is determined by system geometry and fidelity requirements and is not compromised by either calculation cost or stability constraints. An implicit numerical technique is used to ensure stable response under all conditions.
An ANTHEM™ model is graphically created and maintained in the Orchid® Modeling Environment graphical simulation environment. The seamless integration with Orchid® Modeling Environment provides a number of significant advantages including:
- Graphical model design
- Model and code standardization
- Multiple model configurations
- Integrated tracking of calibration and reference data
- Superior graphical testing and visualization environment.
ANTHEM™ has been proven successfully on nuclear and fossil-fueled plant simulators worldwide.
Related Solutions

Certifications | L3Harris Montreal, Canada
LEARN MOREAffiliations
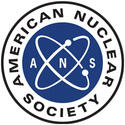
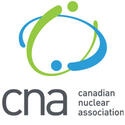
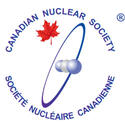
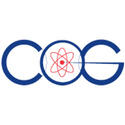
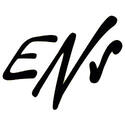
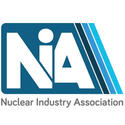
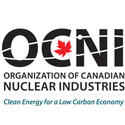
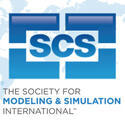

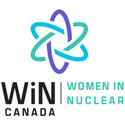
Related News
Related Domains & Industries
Contact Us
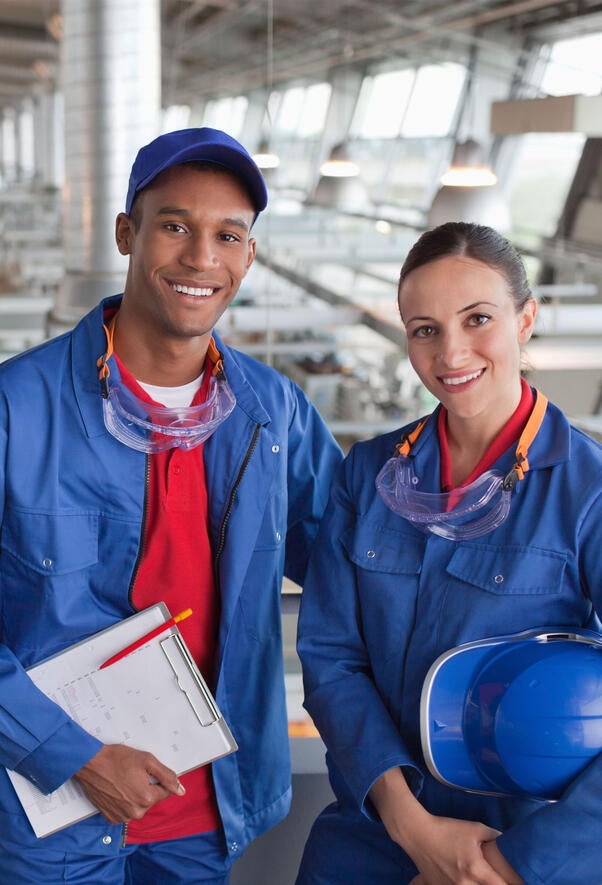